When selecting the right air motors for any given application, it is advisable to consider what needs must be satisfied.
Air motors are flexible powerhouses capable of driving a wide range of applications in the realms of industrial automation and manufacturing. However, with so many alternatives available, choosing the appropriate air motor may be difficult. This article will serve as a guide to help you make an informed decision, ensuring that the air motor you select meets all your needs.
It is likely that multiple different motors might operate at the same working point due to the air motor’s large operating range. Where you locate the working point on the torque-speed curve will have an impact on the motor you choose. The smallest choice is to choose the one that provides the greatest power at the closest feasible distance to the working point since it is most efficient to operate the motor at the speed of maximum power. For a given power output, this motor will also provide the least amount of air consumption.
If the air motor’s consistent speed is crucial, working at speeds below the point of maximum power should be avoided. This guarantees that there will be some “reserve power” in the event of an increase in load. When the torque requirement is unclear, it is also a good idea to operate closer to the idle speed.
The stress on the gears is significant due to low speed and high torque. The lifespan of the vanes is impacted by high speeds. A big motor that is limited or operated at low pressure should be considered if a very long lifespan is required.
Operational Parameters: Meeting Specific Requirements
Normally, operating parameters are adequately described by giving the required torque and corresponding speed. However, six common additional requirements frequently occur:
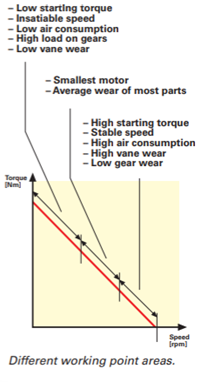
- The motor must start up with a specific torque
A motor must start up with at least a threshold torque for many applications. When a motor is used to move a weight, this may be the case. The tabular data must be searched for the minimal starting torque for a certain motor.
- The motor must achieve the required free speed and stall torque
Tools for installing threaded connections and strapping for packing are two prominent uses for air motors. Both applications have requirements for stall and free speed. The process’s speed is determined by its free speed. For example, when picking up the slack during strapping and the rundown during screw attachment, the engine is frequently operating at low torque. The strap tension and the torque of the threaded joint are determined by the stall torque.
- Service horizon
The working environment has a significant impact on a motor’s service life. The service life of lubricated vanes for vane motors is normally 2000 hours, while the service life of lubrication-free vanes is 1000 hours if the operating cycle is a mixture of free running, running at full power, and breaking down to stall.
Based on the suggested time intervals, we advise an initial assessment to estimate the service life more precisely. The maximum permitted vane wear for each motor type and size is listed in the product instructions that came with the motor. Before the wear surpasses these levels, a change of vanes is advised.
- Consumption of air
When minimal air consumption is a top goal, finding the smallest motor should be your top focus. If you have chosen a motor size and have alternatives within this size, you should be aware that the air consumption will be larger the closer the motor runs to its free speed. If you decide to modify a motor’s performance, restricting airflow (at the motor intake) will result in a lower air consumption than regulating pressure.
- Shaft operation
The Air Motor Catalogue lists the maximum permissible shaft load for each motor. Shaft loading codes are included in the data tables. These codes point to curves that provide the permitted radial and axial shaft load combinations. Checking that the application won’t produce shaft loads over what we permit is a good idea. In extremely unusual circumstances, you might need to use a bigger motor to handle the shaft loads.
Benefits of Different Air Motors Types
In addition to selecting the right air motor, it’s important to consider the benefits of different motor types, including:
- Piston Motors: Piston air motors offer precise control and a high power-to-weight ratio, making them suitable for applications that require accuracy and power. Their ability to operate at low speeds and high torques makes them ideal for heavy-duty tasks. They are often chosen when consistent speed and reliable performance are critical.
- Turbine Motors: Turbine air motors excel in applications where high speed and minimal air consumption are essential. They are known for their lightweight design and can deliver rapid acceleration and deceleration. Turbine motors are preferred when tasks demand agility and rapid response.
- Vane Motors: Vane air motors provide a balanced combination of power, speed, and efficiency. They are versatile and well-suited for a wide range of applications. Vane motors are often chosen for their reliability and ease of maintenance, making them a popular choice in various industries.
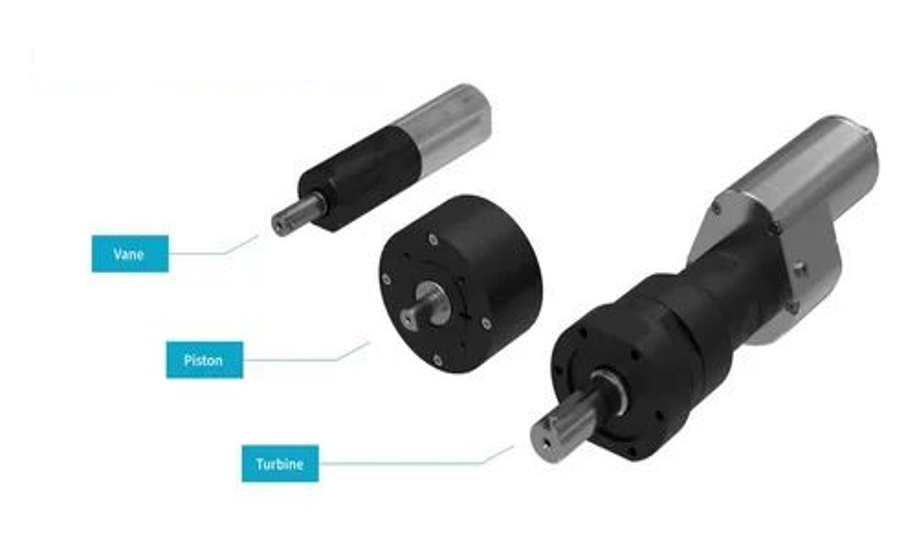
A careful balance between performance, application requirements, and environmental considerations is necessary when selecting the best air motor. You may confidently make a choice that boosts productivity and efficiency in your operations by identifying your demands, comprehending the many types of motors, taking performance characteristics into account, and taking supply, environment, and integration factors into account. Power is important, but choosing the best air motor also requires accuracy and task-specific optimization.
For further insights and detailed technical information, consult the Pocket Guide to Air Motors by Atlas Copco or Contact us directly.