In several industrial fields, air motor have proven themselves to be dependable and adaptable workhorses. Air motors provide effective and reliable motion for industrial and aeronautical settings. Engineers and developers have studied a variety of methods for expanding the capabilities of these pneumatic miracles to optimize performance. This article explores techniques for modifying the performance of air motors, opening new possibilities for efficiency and power.
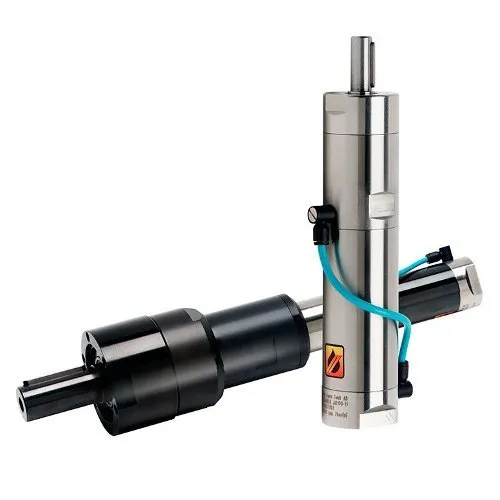
Optimizing Performance One PSI at a Time: A User’s Guide
The key to improving air motor performance is air pressure adjustment. This method works on the straightforward premise that increased pressure causes the air inside the motor’s chambers to expand more forcefully. Increased rotational speed and torque follow, which eventually improve overall performance. To avoid inefficiencies or safety hazards, it is crucial to determine the ideal pressure balance. The air motor performs at its maximum and produces amazing results with proper tuning.
Tailoring Power to Your Needs: User’s Control
The rigorous control of airflow is part of the art of altering the performance of air motors. Engineers may adjust the compressed air motor’s flow rate to adjust the motor’s speed and torque output to meet specific needs. When jobs require different levels of power, this degree of control is quite useful. Airflow control enables you to precisely adjust performance, whether it’s a delicate job requiring finesse or a tough activity demanding raw force.
Vane and Rotor Design: Manufacturers’ Expertise
We come across the vane and rotor design as we go further into the air motor’s core. These components’ innovations have a significant impact on performance. To decrease friction, improve air sealing, and increase overall efficiency, engineers’ experiment with vane forms, materials, and rotor assembly methods. These little but significant changes lead to higher production and longer operating life, demonstrating the importance of technical expertise in performance improvement. Technical expertise from manufacturers plays a pivotal role in performance enhancement.
Navigating Efficiency: User and Manufacturer
An essential part of performance improvement in the world of mechanical systems is adequate lubrication. Components of an air motor with good lubrication operate more smoothly and perform better because friction and wear are decreased. A crucial factor is choosing the proper lubricants that can resist the rigorous conditions within the motor while retaining maximum efficiency. It’s noteworthy that modern markets offer lubrication-free versions, providing an alternative that eliminates the need for lubrication maintenance. A properly maintained motor, whether lubricated or lubrication-free, orchestrates a seamless performance akin to a harmonious symphony.
Consistency Matters: Manufacturers’ Expertise
Temperature variations can affect the operation of air motors. Air density may decrease as temperatures rise, decreasing the motor’s output. By including cooling systems in air motor designs, engineers can overcome this difficulty and guarantee reliable performance even in a variety of climatic conditions. This focus on temperature control highlights our dedication to upholding efficiency and dependability everywhere.
Material Selection: Manufacturers’ Expertise
The construction materials used for air motors have a significant influence on how well they work. Durable, lightweight materials help lower the weight of the motor, which improves efficiency and reaction times. For demanding applications to succeed, materials with high temperature and pressure tolerance are essential. Building air motors that can survive the demands of modern industry relies heavily on material selection.
Harnessing Precision: User’s Realm
The world of sophisticated control systems. Engineers may dynamically change air pressure, airflow, and other factors by combining sensors, feedback loops, and electronic control units. Because of their increased flexibility, air motors are now able to adjust their performance in a precise way to meet changing demands in real-time.
Innovation in Components: Manufacturers’ Role
In the field of air motor technology, innovation is encouraged. The performance of air motors has evolved because of internal component redesign, particularly regarding vanes, rotors, and chambers. Engineers may tune these components for higher efficiency and overall performance using cutting-edge modeling and advanced techniques, including computational fluid dynamics (CFD) simulations. Manufacturers continuously drive performance advancements through innovative component design.
In summary, optimizing air motor performance is a collaborative effort, involving both user adjustments and manufacturer expertise. Users can fine-tune performance through pressure and airflow control, while manufacturers play a crucial role in optimizing design, selecting materials, and implementing innovations. Together, these efforts unlock the full potential of air motors, enabling enhanced efficiency and power across diverse applications.
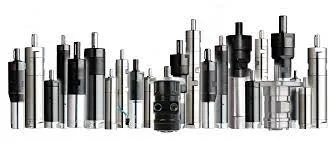
A journey of science, engineering, and creativity is required to change the performance of an air motor. Each method used creates an air motor that sets new benchmarks for the industry through a symphony of efficiency and power. The techniques examined here highlight the never-ending pursuit of perfection in air motor performance modification, ranging from altering air pressure to manufacturing cutting-edge components. By using these methods, businesses may fully utilize air motor technology and advance their operations into a world of increased power and efficiency.
Are you looking for more information? If you have any questions, feel free to reach out to us anytime.