Where the ATEX standard originated.
Concerning coal
The Second Industrial Revolution relied heavily on the availability of coal, so coal mining and extraction were essential to its continuation. As a result, countries like Belgium, France, the United Kingdom, and Germany that were going through this process quickly learned about one of the inherent risks associated with this activity: fire damps, or accumulations of methane and other similar gases in coal mine tunnels.
The same natural processes cause the creation of coal and methane; under high pressures, such as those present in natural coal resources, bituminous coal tends to adsorb methane on its surface. When the pressure is relieved, as in a mining operation, the coal begins to expel methane, along with other chemicals such as ethane, carbon dioxide, and hydrogen sulfide.
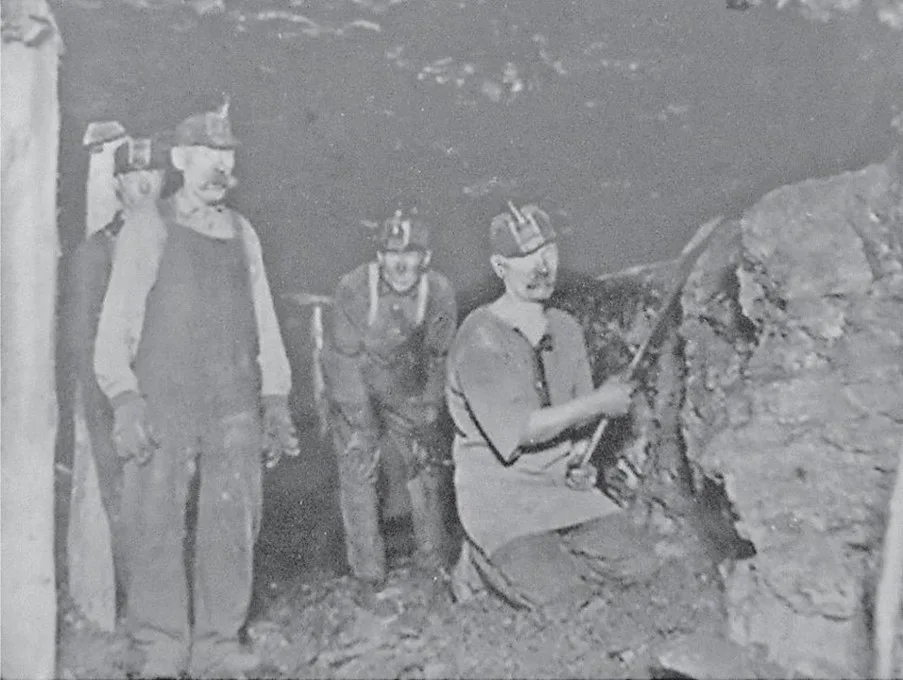
All these compounds can form potentially explosive atmospheres if oxygen is available in the mine’s environment, and the issue is exacerbated if coal dust in suspension is present. All these variables combined to produce exceedingly hazardous working conditions in typical coal mines of the second half of the nineteenth century.
Coal miners were most afraid of finding fire damps since the industry’s first reaction to big and dangerous coal mine gas accumulations was to burn them immediately using any available ignite source.
Although the unfortunate miners chosen for this duty wore safety masks and were covered with damp towels, the long-term viability of this endeavor was questionable due to the high fatality rate.
Using safe lights was the first step taken to stop fireworks explosions because they were an inevitable and necessary instrument for mining.
A safety-focused scientific methodology
Sir Humphry Davy invented the first safe lamp in 1815. It was intended to function without running the risk of becoming an ignition source. The two fine metal mesh coverings around the flame of the Davy lamp prevented it from becoming an ignition source. The meshes’ openings were big enough to allow air to reach the flames, but not so big that the flames could escape into the surrounding air.
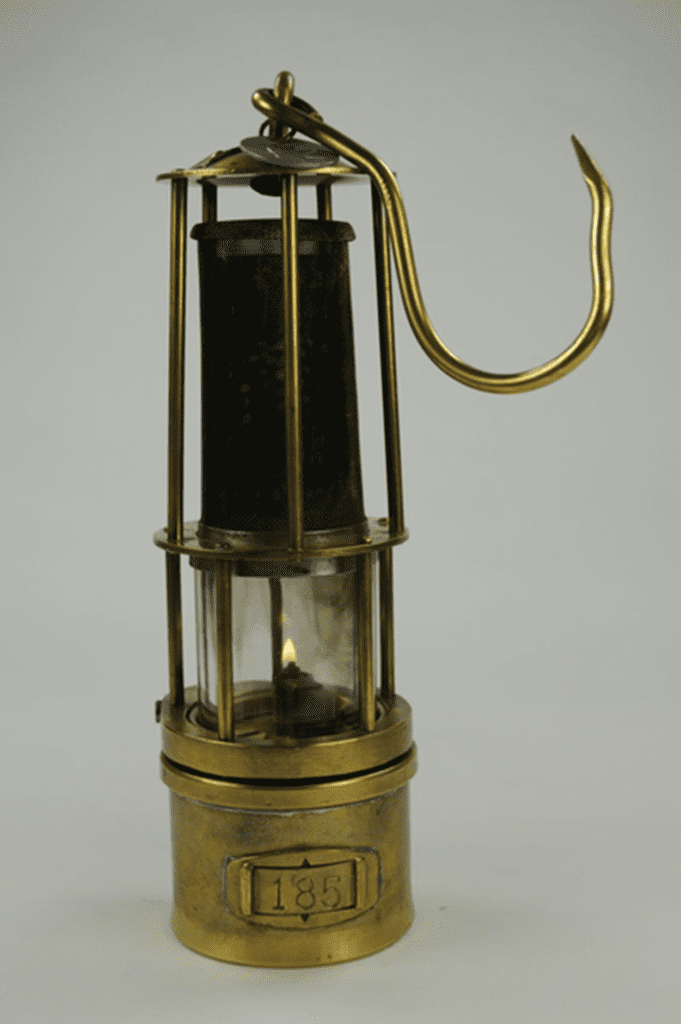
It was the first time a flame arrestor had been used as a safety precaution to prevent explosions in a dangerous region.
This incident had a significant impact on the advancement of explosion protection techniques across Europe. The European approach to explosion prevention in high-risk environments has always been to create workable ways to use devices that have the potential to ignite in a safe manner without compromising their utility. Electrical machinery was first used in coal mine shafts around 1870. The UK saw the installation of electrical lights for the first time in 1882. The first tests of flameproof enclosures were conducted between 1884 and 1885 because of concurrent advances in Germany and the UK.
An inherently sound concept
On October 14, 1913, a major explosion occurred in the Senghenydd Collery in South Wales, killing 439 miners.
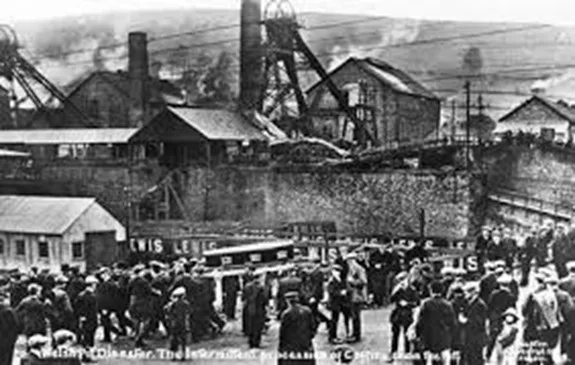
The British Home Office Experimental Station at Eskmeals later determined that an electrical signaling bell caused the explosion, with the spark originating from it. Further investigation, conducted with the assistance of Durham University, revealed that the release of energy from the inductive solenoid triggering the bell caused the spark.
Upon making this discovery, the researchers concluded that reducing the supply voltage to 24 volts and limiting the current with a non-inductive resistor could decrease the energy. This adjustment would render the circuit safe to operate, provided that the total energy in the circuit was insufficient to function as an ignition source for the surrounding atmosphere. This led to the establishment of the concept of an inherently safe circuit.
The German approach to problem-solving
The German PTB (Physikalisch-Technische Bundesanstalt, also known as the National Metrology Institute), an organization founded to standardize units in electrical value measurement, was making comparable progress. Names like Hermann von Helmholtz and Werner von Siemens were on the PTB’s original membership list. Max Planck and Albert Einstein were both PTB workers at one point in time.
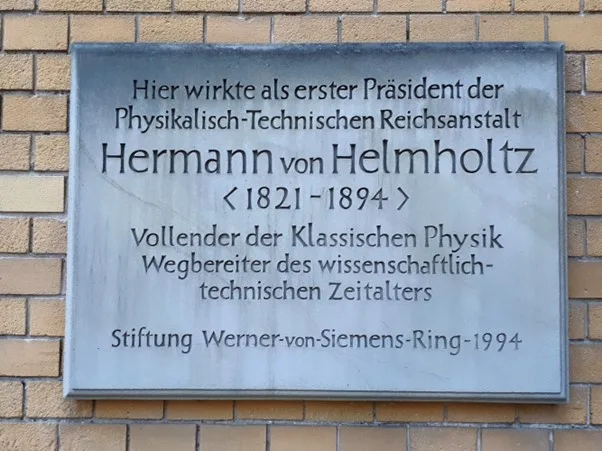
The VDE (Verband Deutstcher Elektrotechniker, or German Association of Electro engineers) developed the first set of guidelines and criteria for firedamp hazardous mines in 1912; this was the VDE 0170 standard.
The DKE (German Commission for Electrical, Electronic, and Information Technologies), established through an agreement between the VDE (Association for Electrical, Electronic & Information Technologies) and DIN (German Institute for Standardization), actively creates and approves safety guidelines and standards in those areas. Together, the VDE, DIN, and DKE function as a single organization.
The British Standards Institute in the United Kingdom released BS 229-1929 in 1929, which was the first British standard for flameproof equipment. The phrase “flameproof” in this article implies that an explosion is contained and that the enclosure puts out the explosion’s flames. The phrase “druckfeste” in German, which denotes flameproof enclosures, is where the letter “d” originates.
“Leitsätze für die Errichtung elektrischer Anlagen in explosionsgefährdeten” (Guidelines for the installation of electrical systems in potentially explosive areas) is the name of the 1935 VDE 0165 standard, published by the VDE. This standard is the first to distinguish between atmospheres containing dust and those containing flammable gases and vapors.
The VDE divided the standards for product design (VDE 0170/0171) and installation (VDE 0165), a practice that has persisted to this day. The forms of fundamental explosion protection, such as flameproof, oil immersion, and enhanced safety, were also described in this standard.
Two routes leading to the same location.
The UK and German standard organizations conducted their own tests at the same time as the UL laboratories were performing the Maximum Experimental Safe Gap (MESG) measurements using the Westerberg test equipment. However, they used a spherical test apparatus for their measurements.
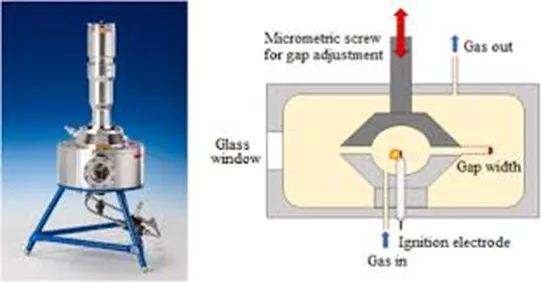
As a result of the divergence, the MESG dimensions used in ATEX and IECEx continue to be different from those used in the US.
In response to the need for weathering resistance in components installed inside flameproof enclosures, a safety protection technique was developed to address corrosion concerns arising from the presence of MESG.
Things begin to become worldwide after the conflict.
All these improvements were hampered by the Great Recession and World War II, when world trade came to a halt. However, following WWII, Europe began an integration process with the development of the European Common Market, which led to the formation of the European Community.
Setting aside the political implications of this process, it became evident over time that promoting business trade across EC states required a common set of standards. The countries with the most experience using electrical equipment in hazardous areas, which happened to be the EC’s largest economies, heavily influenced the subsequent process of standards unification that began in the 1970s. The German Standards Institute DIN and the British Standards Institute BSI played a significant role in shaping this process.
In 1972, this standardization initiative achieved its first breakthrough when a new set of regulations, known as EN (Europäische Norm or European Standard) 50014 to 50020, superseded all local rules for the use of explosive devices.
The EU adopts the ATEX Directive.
Established in 1973, the Belgian-based CENELEC European Standards Organization aimed to facilitate commerce between EC members and uphold the initial set of harmonized standards. In 1975, CENELEC issued the first directive for hazardous-area devices, followed by the release of installation criteria in 1978.
This triggered a series of multinational agreements, culminating in the publication of the ATEX Directive 94/9/EC in 1996, also known as “ATEX 95” or the “ATEX Equipment Directive,” and the Directive 99/92/EC, also known as “ATEX 137” or the “ATEX Workplace Directive,” both of which became EU law.
The acronym ATEX originates from the French standard 94/9/EC, which translates to “Appareils destinés à être utilisés en ATmosphères EXplosives” or “Devices to be used in explosive atmospheres.” The European Parliament issued the most recent modification to the ATEX Directive on March 29, 2014, known as the 2014/34/EU version. It refers to the harmonization of national legislation governing equipment and protection systems intended for use in potentially explosive environments.
Are you looking for more information about the ATEX Directive? If you have any questions, feel free to reach out to us anytime.
For further insights and detailed technical information, consult the Pocket Guide to Air Motors by Atlas Copco or Contact us directly.