Efficiency, dependability, and accuracy are critical in the field of industrial maintenance. Air motors are one technology that has helped achieve these needs. These adaptable gadgets have found use in a variety of industries, from manufacturing and automotive to aerospace and mining. In this article, we will look at the advantages of air motors in industrial maintenance and how they help to increase production and decrease downtime.
Air motors, also known as pneumatic motors, are mechanical devices that transform compressed air into mechanical energy that may subsequently be utilized to accomplish a variety of tasks. They work on the premise of using compressed air expansion to generate rotational motion, making them suitable for a wide range of industrial applications.
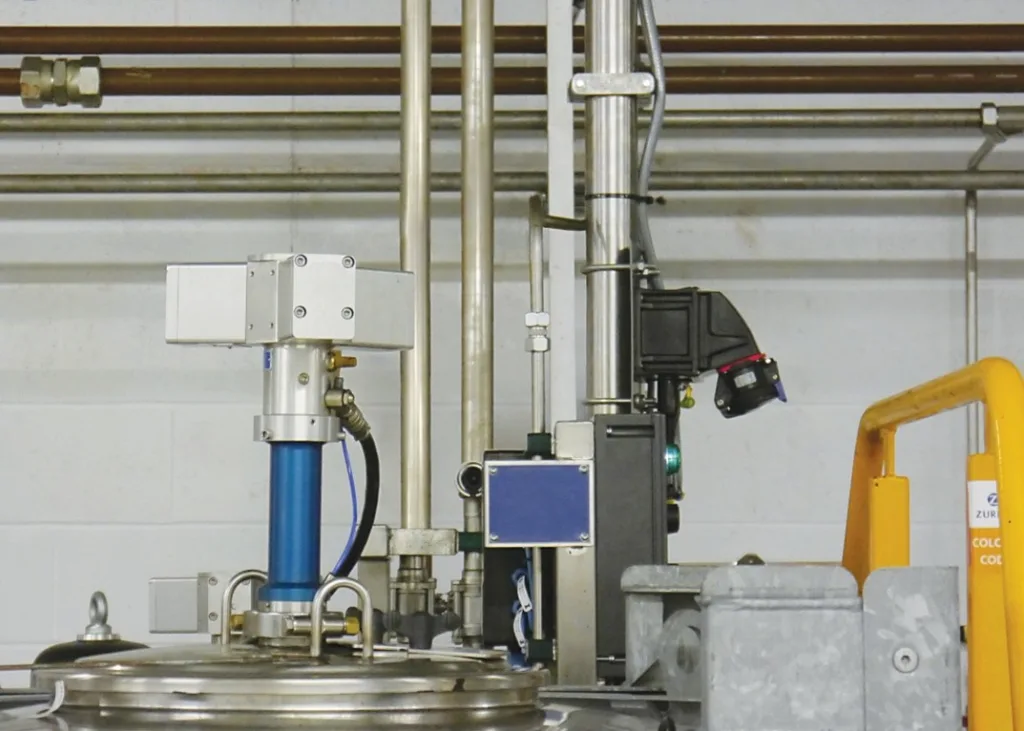
Air Motors in Industrial Maintenance
- Air motors are well-known for their high power-to-weight ratio. They are lightweight while still giving high power output, which is critical for activities requiring mobility and maneuverability. Because of this, they are useful for a broad range of applications, including powering hand tools and operating conveyor systems.
- Air motors are a safe alternative in businesses where the presence of combustible gases or dust is a problem, such as chemical plants and oil refineries. They are fundamentally safe since they do not emit sparks or heat when operating, lowering the danger of explosions and fires.
- Air motors provide accurate speed and torque control, enabling for tiny changes in industrial maintenance activities. When dealing with delicate or detailed operations, such as assembly line procedures or equipment maintenance, this degree of control is important.
- Air motors are well-known for their dependability and longevity. They have fewer moving components than typical electric motors, which means they last longer. This endurance reduces the need for regular replacements and maintenance, decreasing operational expenses in the long run.
- Air motors require less maintenance than electric motors. They are less prone to damage from overload circumstances and can operate in tough locations without deteriorating performance. This implies there will be less downtime for maintenance and repairs.
- By altering the air pressure or the control valves, air motors are easily adaptable to a variety of applications. They are excellent for a variety of jobs because of their adaptability, including running grinders and cutting instruments, as well as pumps and agitators.
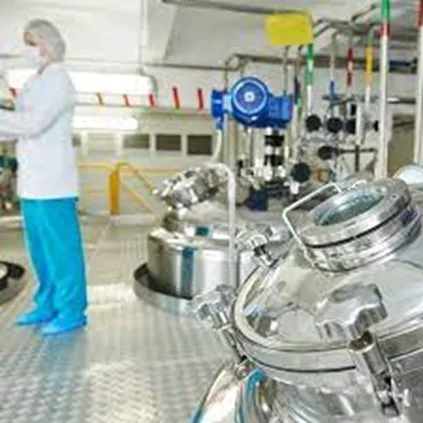
Applications in Industrial Maintenance
Numerous industrial maintenance activities use air motors, including but not limited to Air motors enable maintenance workers to operate effectively by powering a range of portable instruments, including grinders, sanders, and impact wrenches. Conveyor belts are driven by air motors, enabling the transportation of materials and goods inside production facilities. In sectors like food processing and pharmaceuticals, they are used in mixing and agitation procedures to guarantee constant product quality. Air motors are used to precisely regulate the flow of fluid by activating pipeline valves. Air motors are used in hoists and winches to transport equipment and materials securely during maintenance activities demanding heavy lifting.
Because of their effectiveness, dependability, and adaptability, air motors have established a niche in industrial maintenance. They are essential tools for maintenance specialists due to their excellent power-to-weight ratios, fine control, and longevity. Air motors help boost output, cut downtime, and ensure safer operations in any industry, whether manufacturing, petrochemicals, or elsewhere. We may anticipate that air motors will play a bigger part in industrial maintenance in the future as technology develops.
Are you looking for more information? If you have any questions, feel free to reach out to us anytime.