Designed to provide outstanding starting and low speed performance
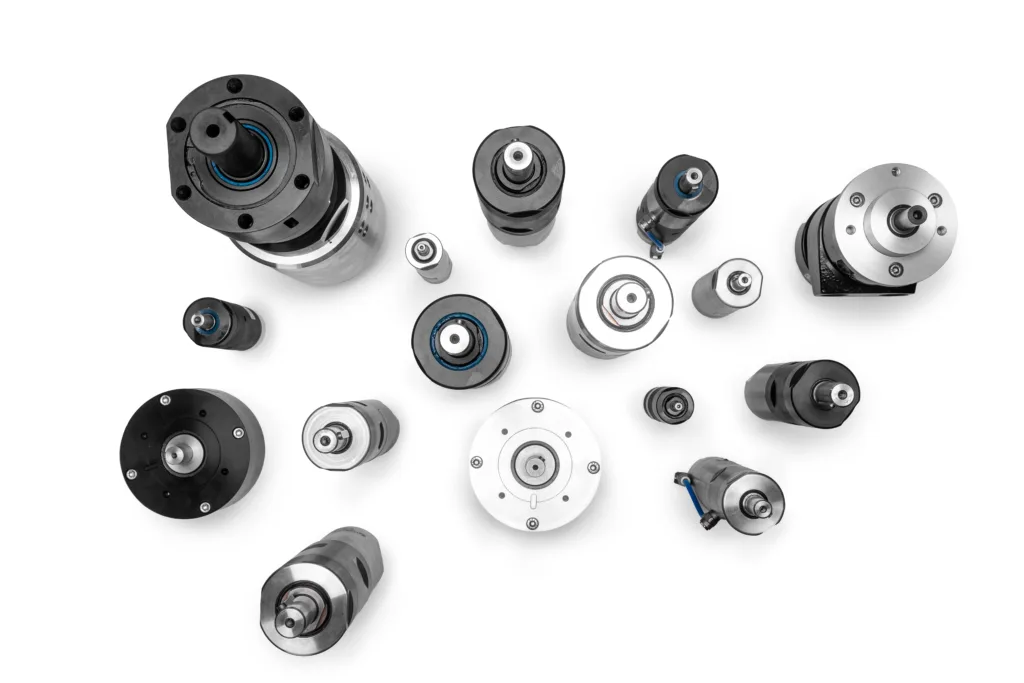
LZL vane motors are available in five sizes, offering outputs of 1.05 kW, 1.3 kW, 2.3 kW, 3.4 kW and 5.2 kW, respectively.
They are designed to give outstanding starting and low-speed performance. This is achieved by using a six-vane motor and by optimum vane/cylinder sealing, obtained through a combination of ‘vane air’ and interconnecting pins.
Featuring few components, these motors are ruggedly constructed and offer a long service life.
General Overview
Atlas Copco LZL vane motors use six vanes and optimum cylinder sealing for a rugged, compact design that offers a long service life. Certain models are available in standard and stainless-steel versions. The motors have strong starting torque and can be run non-reversible or reversible with lube free vanes.
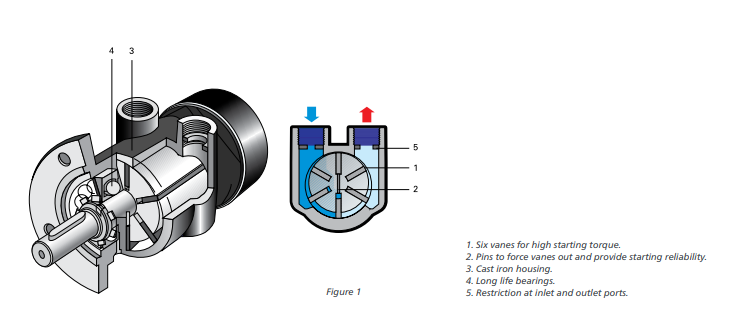
Features
- IEC and NEMA mounting options
- Lubrication free
- Reversible
- Stainless steel is available
- Good low speed characteristics
- ATEX certified
Benefits
- Reliable starting
- Strong bearings
- Long vane life
- High radial and axial load capacity
Design
A slotted rotor rotates eccentrically in the chamber formed by the cylinder and cylinder end plates. Since the rotor is off-center and its diameter is smaller than that of the cylinder, a crescent-shaped chamber is created. The rotor slots are provided with vanes that move freely to divide the chamber into separate working chambers of different sizes. As a result of the centrifugal force, which is often reinforced by the compressed air, the vanes are forced against the cylinder wall to seal the individual chambers. The actual efficiency of these seals is a function of what is called ”internal leakage”.
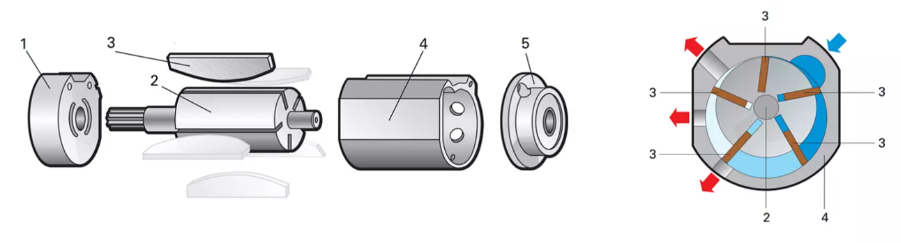
Working principle
A. The air enters the inlet chamber “a”. Vane 2 has just sealed off the chamber “b” between itself and vane 3. The pressure in chamber “b” is still the inlet pressure. This pressure acts on vane 3, moving it in a clockwise direction.
B. The vanes have rotated further and the expansion process in chamber “b” has started. The pressure in it is thereby reduced but there is still a net force moving the rotor forward as the area of vane 3 is larger than the area of vane 2 in chamber “b”. Furthermore the inlet pressure acts on vane 2 in the inlet chamber “a”.
C. The vanes have moved further. Chamber “b” is now being emptied through the outlet and there is no more contribution from this chamber. The force moving the rotor forward now comes from the force on vane 1 and vane 2.
Thanks to this simple principle the energy of the compressed air is converted into rotational motion from chamber to chamber, and the motor turns.
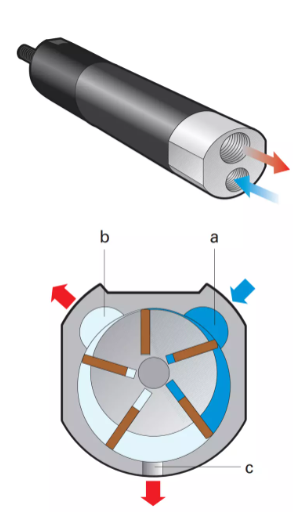