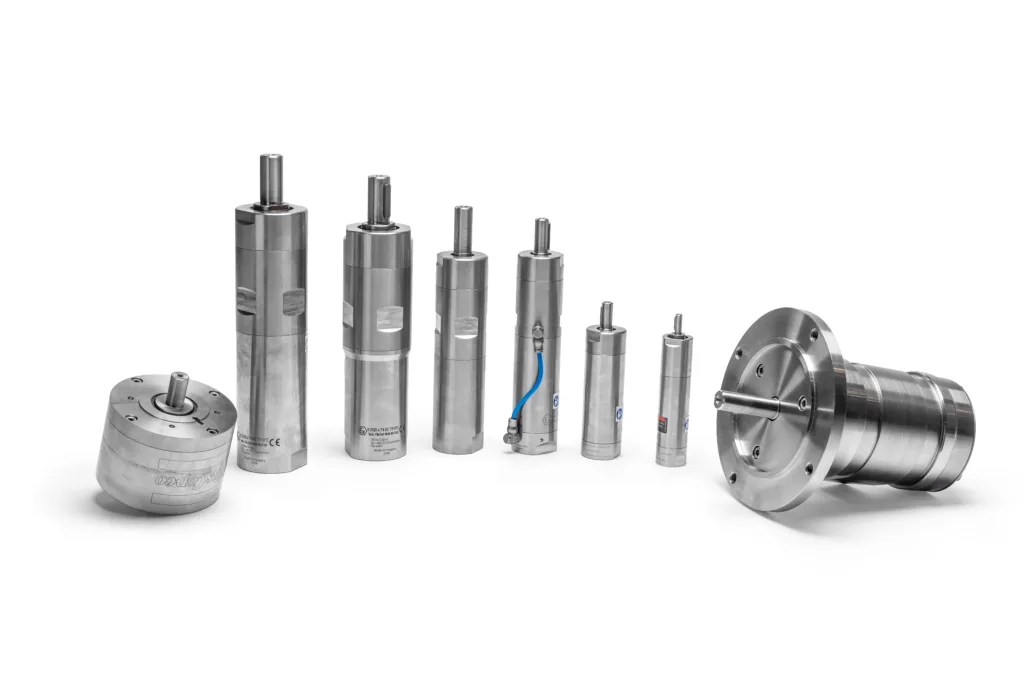
Air motors from Atlas Copco are a reliable, cost-effective solution when applying power to rotating machines. Consider the air motor features and characteristics that give a large number of benefits to the designer:
- Power-to-weight performance that is superior to most other motors is in fact, 75% lighter and 85% smaller than an asynchronous electric motor with the same output.
- Can be held stalled at full torque indefinitely, and accepts repeated starting and stopping without limitation.
- Torque, speed, and direction of rotation can be changed easily using simple control methods.
- Output that automatically adjusts to match the applied load.
- Controllable over a wide speed range.
- Ideal for many applications in hazardous or hostile environments.
- Smooth start-up to minimize “shock” loading on transmission components.
- Unaffected by, and will not generate, electrical interference.
General Overview
Atlas Copco LZB vane motors utilize five vanes to ensure excellent starting and low speed performance. Most models come in standard and stainless-steel versions to match your application’s specific need. The long and slim design integrates seamlessly with several different mounting styles, while multi-step planetary gears dial in your exact torque and speed requirements, offering high efficiency with compact dimensions
Features
- Long and slim
- Fit with major standard mounting
- Lubrication free
- Reversible
- Brake available
- Stainless Steel range
- High torque and low speed range
- ATEX certified
Benefits
- High power-to-air consumption ratio
- High reliability
- Low air consumption
- Long vane life
Design
- A slotted rotor rotates eccentrically in the chamber formed by the cylinder and cylinder end plates.
- Since the rotor is off-center and its diameter is smaller than that of the cylinder, a crescent-shaped chamber is created.
- The rotor slots are provided with vanes that move freely to divide the chamber into separate working chambers of different sizes.
- As a result of the centrifugal force, which is often reinforced by the compressed air, the vanes are forced against the cylinder wall to seal the individual chambers.
- The actual efficiency of these seals is a function of what is called ”internal leakage.”
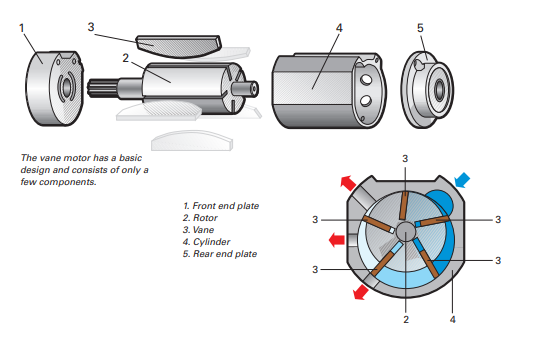
Working Principle
A. The air enters the inlet chamber “a”. Vane 2 has just sealed off the chamber “b” between itself and Vane 3. The pressure in chamber “b” is still the inlet pressure. This pressure acts on vane 3, moving it in a clockwise direction.
B. The vanes have rotated further, and the expansion process in chamber “b” has started. The pressure in it is thereby reduced, but there is still a net force moving the rotor forward as the area of vane 3 is larger than the area of vane 2 in chamber “b”. Furthermore, the inlet pressure acts on vane 2 in the inlet chamber “a”
C. The vanes have moved further. Chamber “b” is now being emptied through the outlet, and there is no more contribution from this chamber. The force moving the rotor forward now comes from the force on vane 1 and vane 2.
Thanks to this simple principle, the energy of the compressed air is converted into rotational motion from chamber to chamber, and the motor turns.