Pneumatic motors, also known as “air motors,” employ compressed air to produce rotating motion. They are frequently employed in industrial settings that need a reliable and durable drive motor, such as the chemical and pharmaceutical industries.
The chemical and pharmaceutical sectors are known for demanding safety, accuracy, and efficiency standards. Manufacturers of equipment in this industry are increasingly resorting to modern technology to meet industry demands. The use of air motors is one such technology that is making considerable advances in these sectors. These tough and adaptable drives are proving essential in a broad range of applications, from mixing and agitating to pumping and tensioning, while satisfying the stringent requirements of these industries. In this essay, we will look at how important air motors are in chemical and pharmaceutical applications.
Air motors, or pneumatic motors, provide mechanical energy by converting compressed air into a rotational force. Industries, particularly in the chemical and pharmaceutical sectors, have long utilized this technology because of its inherent robustness. Air motors are useful for a range of activities in various sectors due to their simplicity and efficiency.
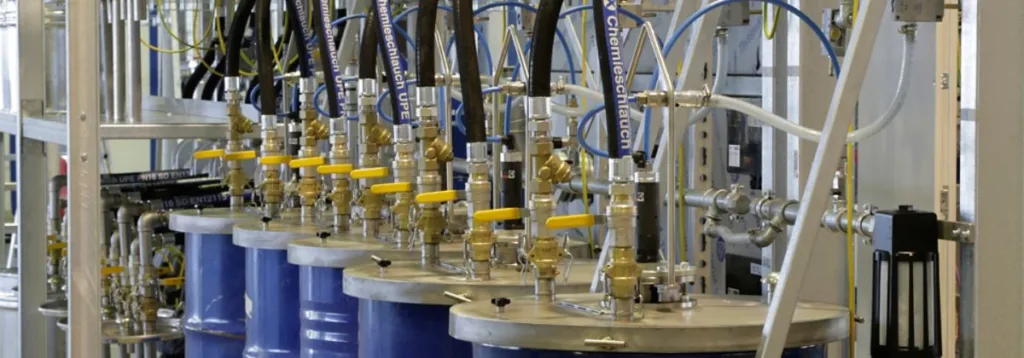
For usage in chemical and pharmaceutical applications, air motor provide several benefits over other type of motor, including:
- Safety: Air motor are safe since they do not create heat or sparks. As a result, they are ideal for use in hazardous environments such as chemical and pharmaceutical plants, where flammable gases and liquids are prevalent.
- Robust design: Air motor can withstand harsh operating conditions such as chemical, dust, and moisture exposure. Therefore, these motors are ideal for application in chemical and pharmaceutical plants, where equipment consistently faces harsh conditions.
- Controllability: Because air motor are highly controllable, they are ideal for applications needing precise speed and torque control. This is critical for a range of chemical and pharmaceutical mixing, blending, and dispensing procedures.
- Minimal maintenance: Because air motor require less maintenance over time, they are a cost-effective solution. This is critical in chemical and pharmaceutical production plants, where costly equipment downtime may occur.
- ATEX-compliant: One of the key benefits of air motor in chemical and pharmaceutical applications is their inherent safety. Air motor do not produce sparks when operating, making them appropriate for usage in potentially hazardous settings, including combustible gases or liquids.
- Clean and contamination-free: Unlike standard electric motor, many air motor are available with vanes that do not require lubrication, which may bring pollution into delicate operations. This function guarantees that air motor are clean and pure, which is critical in pharmaceutical manufacturing.
- Reliability and Durability: Air motor is well known for their durability and dependability. They can function in severe situations, including hot temperatures and corrosive environments, without significantly reducing performance or longevity.
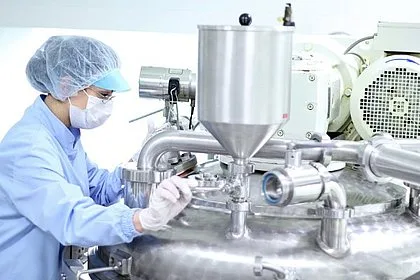
In chemical and pharmaceutical manufacturing facilities, air motor is used for several purposes, including:
- Mixing and Agitating:
Air motor is commonly used in the mixing and agitation of chemicals and pharmaceutical ingredients. They ensure thorough blending while preventing contamination or ignition risks.
- Pumping and Conveying:
Air motor is used in pumps and conveyors to transfer liquids, powders, or granules safely and efficiently. Their ability to handle viscous fluids makes them particularly useful in this regard.
- Dispensing and Filling:
Precision dispensing and filling of liquids and powders are essential processes in pharmaceutical manufacturing. Air motor provide accurate control over these processes, reducing waste and ensuring consistency. - Cleaning and Sterilization:
In cleaning and sterilization equipment where strict hygiene standards are required, operators use air motors. Their ability to operate without lubrication helps maintain a sterile environment.
While air motor have many advantages in chemical and pharmaceutical applications, they are not without their drawbacks. One big problem is the requirement for a compressed air supply, which can use a large amount of energy. Using energy-efficient compressed air systems and preventing air leakage can mitigate this problem.
The future of air motor in these areas is bright. Researchers are actively working on increasing the energy efficiency of compressed air systems and developing control mechanisms to enhance accuracy and responsiveness.
In chemical and pharmaceutical manufacturing facilities, air motor are a flexible and dependable form of drive, well suited for many applications. Engineers and technicians may guarantee that their apparatus performs in a secure and effective manner by carefully choosing the appropriate air motor for the application.
Air motors are ubiquitous in the chemical and pharmaceutical sectors, where safety, accuracy, and dependability are critical. They solve a wide range of applications because of their design, cleanliness, and accuracy. As these sectors continue to expand and adapt, air motor will become increasingly important in improving efficiency, productivity, and product quality while adhering to industry safety and regulatory standards.
Are you looking for more information? If you have any questions, feel free to reach out to us anytime.
For further insights and detailed technical information, consult the Pocket Guide to Air Motors by Atlas Copco or Contact us directly.